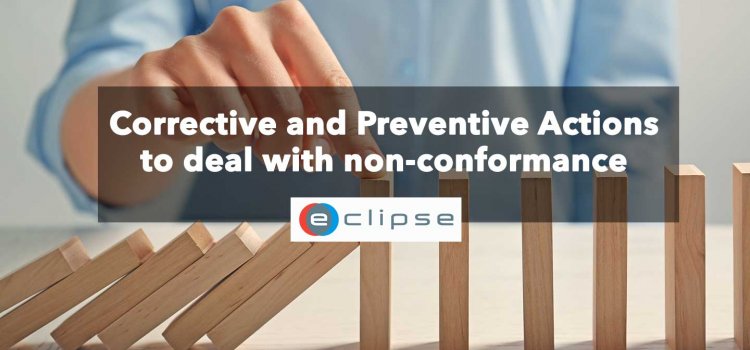
How to Use Corrective and Preventive Action (CAPA) To Deal With Non-Conformance
12 Jun, 2024
Since non-conformance is bound to happen, corrective and preventive action is a necessary aspect of a project or mission. This article discusses the definition of corrective and preventive action, the steps that should be taken to implement the actions, how to implement the steps in your organisation, best practices and ways to improve your workflow.
What are Corrective and Preventive Actions?
Corrective and preventive actions are a series of interventions and steps adopted to prevent the occurrence and recurrence of non-conformances (also known as problems or anomalies) within an organisation or project.
Corrective actions: Involve interventions aimed at correcting or solving non-conformances and make sure they won’t happen in the future.
Preventive actions: These are steps taken to stop non-conformances from happening in the first place.
While typically corrective actions are related to non-conformance reports and preventive actions are related to risk analysing tools. Sometimes after a risk analysis has been done and no preventive action has been taken, corrective action is needed.
The necessity of Corrective and Preventive Actions
Non-conformances can negatively impact the overall operation of a project and company. They could lead to serious problems like financial losses, and reputation crises and greatly impact the brand image of the organization.
When an organization fails to catch up with the right standards and procedures in their workflows and operation, it could also attract the radar of regulatory authorities, create customer dissatisfaction, and so on.
Not implementing corrective and preventive actions to deal with non-conformance could lead to devastating results for the project. To prevent these kinds of problems, it’s imperative for an organization to adopt a series of measures.
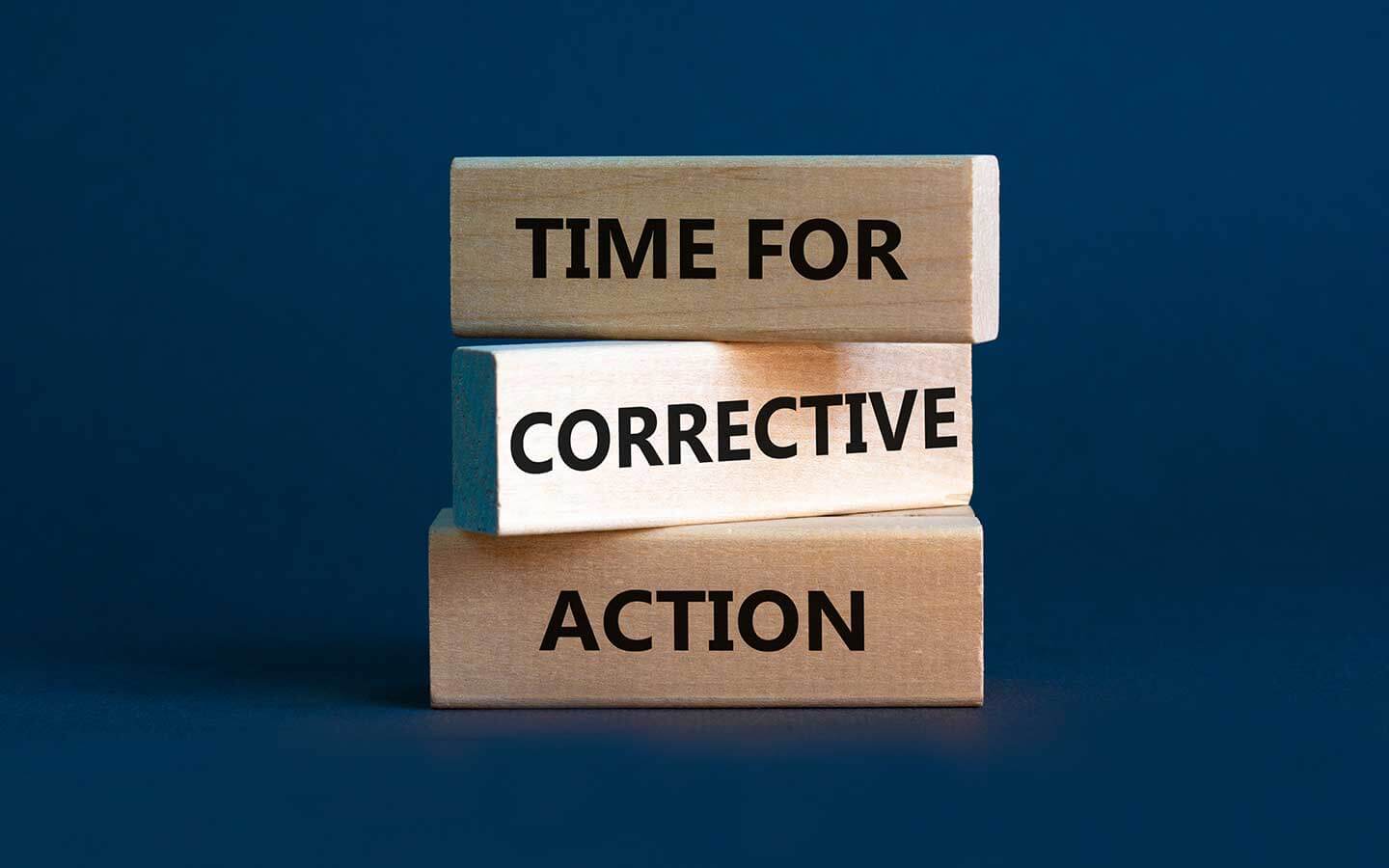
Implementing corrective actions to Non-Conformance
After a non-conformance is found which can be during manufacturing, assembly integration and testing, reviewing, inspection, and even during operation. Corrective action is taken to minimize the impact or to prevent further escalation of the anomaly. Below are some important steps that could be taken when non-conformances occur:
Step 1: Understand the anomaly (analysis)
In order to successfully rectify non-conformances, there needs to be an internal investigation to understand the following. Typically the following questions will be asked initially:
- Why did the problem happen? This could involve digging through the entire organization’s operational workflows to understand the root cause of the problem and how to deal with it.
- Who could be responsible? In order to get to the bottom of the matter, the auditing team has to dig through and identify players that could be responsible for the occurrence of non-conformances. It’s at this point that the findings can reveal whether non-conformances are likely to have happened either due to negligence, ignorance or because of intentional sabotage from rogue actors.
- When did it happen? This helps auditors to know when non-conformances happened and also to better understand the kind of impact it has caused for a defined period of time.
- Where did it happen? This is aimed at identifying and pinpointing where the actual problem could happen. If it affects a specific segment of the organization, then such crucial details could be determined for necessary actions and interventions by the responsible parties
- What is causing it? This could also involve evaluating the organization’s Quality Management framework to see if there are some discrepancies that could be leading to nonconformity within the organization’s workflow.
Now, the definition of the actual problem is important if the successful implementation of the Corrective action is to be realized. During the auditing and investigation process, every detail matters and shouldn’t be taken lightly.
Step 2: Defining the scope of the problem (analysis)
At this point, the auditing team has to understand how big and damaging the problem is. Is it a minor or major problem? Which part of the workflow is affected? Does it happen persistently? Did it happen once and stopped? Which parties are affected? Are our suppliers or customers affected? Does it lead to punitive actions from relevant regulatory authorities?
All these questions are very crucial in trying to understand the scope of non-conformance when it occurs in an organization.
Step 3: Document the problem and define the actions to be taken (planning)
After a comprehensive analysis of the problem has been conducted, and the scope has been determined, it’s time for auditors to document their findings. This is done in a non-conformance report. The documentation of findings helps in achieving two very important objectives:
- It provides an opportunity to refer back to when trying to understand how to deal with similar non-conformance in the future.
- It provides evidence that could be used as a reference point when trying to hold people accountable for their negligence or ignorance.
It’s important to ensure that all findings are captured accurately and stored in a safe place where they can be retrieved easily when needed. This is typically done in a non-conformance tracking system.
Step 4. Contain the non-conformance immediately (action)
After the problem has been identified, if possible you can choose to take a swift intervention to contain the problem from escalating more. This basically involves taking immediate actions as the auditing team continues with their understanding of the problem. This step is crucial for temporary mitigation of the problem but doesn’t necessarily offer the final intervention needed to totally fix it.
Step 5. Broadly study the root cause (analysis)
Further study of the problem can be an effective way to correct complex non-conformances. A way to do this is by doing a root cause analysis. This helps to separate the perceived problem and the actual cause and so, it helps decision-makers in the organization to understand the core of the issue.
Step 6. Planning and implementing the corrective action plan (action)
Now that the non-conformance is fully understood the decision-makers can create an understanding and strategy to solve the problem. This step includes designing and implementing a well-detailed corrective action.
A designated party needs to create a final solution and a brainstorming session might take place to develop options for corrective strategies. After which, decision-makers take actions that solve the problem.
Next to this, the plan contains the kinds of costs and resources associated with executing the adopted corrective action.
The plan needs to be communicated by setting up actions and assigning them to the responsible party, which can be done through action item management.
There has to be a follow-up on the actions and it’s important that all stakeholders are kept in the loop about the corrective action being taken to solve the problem.
Step 7. Evaluation and tracking (analysis)
Evaluation is important to understanding if the adopted corrective action really provided the needed solution to deal with the non-conformances that had been identified. The organization can design a standard monitoring and evaluation framework to help in following the efficiency of the corrective action that was implemented.
Tracking if the non-conformance was solved is another important step in this process. A non-conformance tracking system can help with this and it’s important to assign responsibility to certain individuals so they can be held accountable if the problem persists.
When all these steps have been executed it’s important to close out the case and update all the stakeholders about the status of the corrective action that was taken.
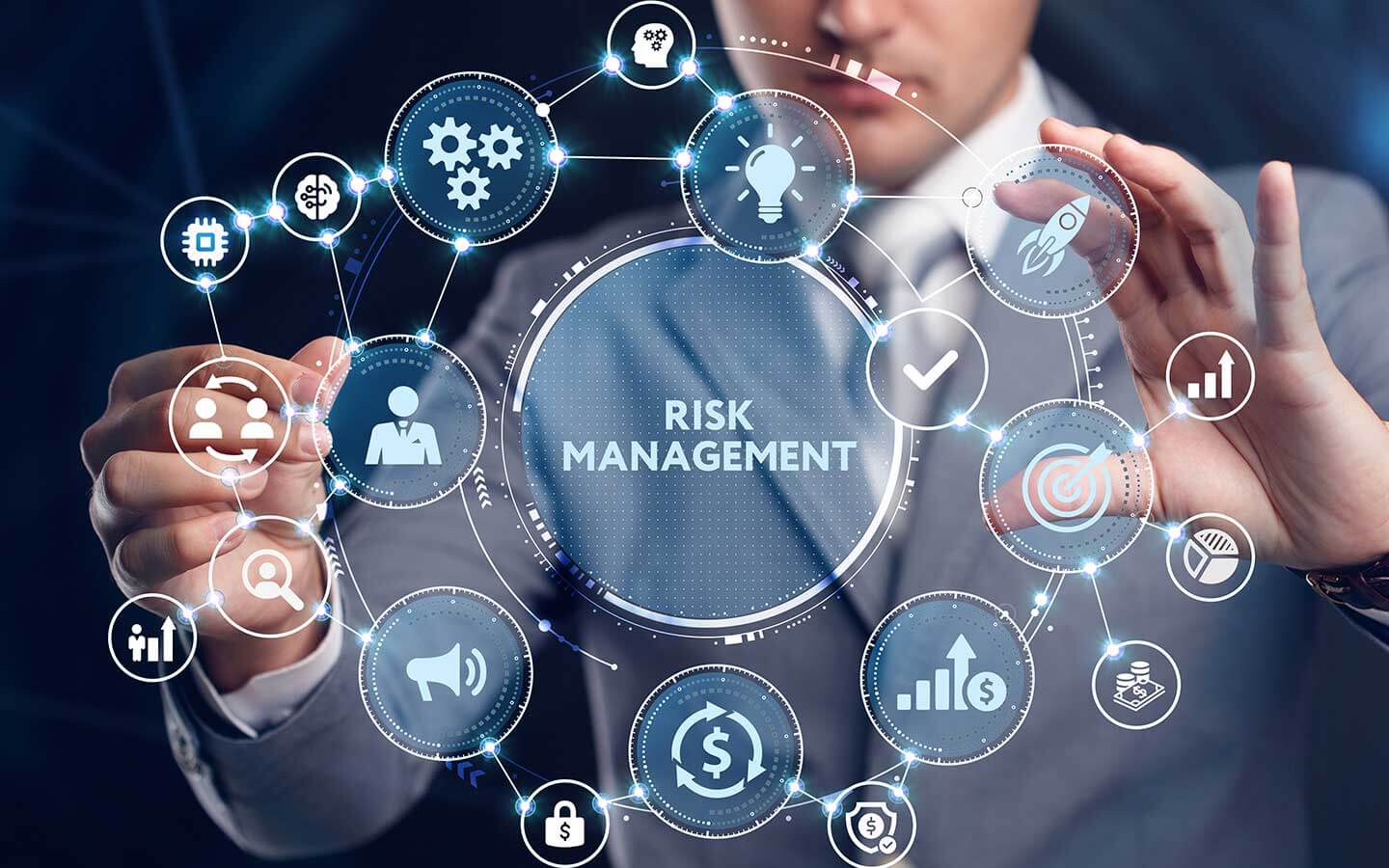
Implementing preventive actions to deal with Non-Conformance
As said earlier, preventive action involves a series of measures that could be employed to deter the occurrence of non-conformance from happening in the organization. Below you can find some key steps including the following:
Step 1: Organizing refresher training for employees
This basically involves skilling the organization’s teams in the areas of quality management and safety guidelines. With this preventative action, the team is trained to adopt better knowledge and skills when it comes to adopting standard operating procedures within the organization’s workflow. When people are properly trained, they will be able to follow an established quality management framework without deviating or compromising on its strictness.
Having a system offers traceability of previous non-conformances, can form the foundation of the previous lessons learned, and will also help to prevent non-conformances from happening in the future.
Step 2: Adopting a standard quality management and standards framework
The organization can have its own internal framework that defines the workflow operating procedures which various players in their respective departments must follow. Adhering to the established operation rules, guidelines and procedures is very important, and so. every organization’s employee is bound to follow them without relenting. The existence of such a framework also creates a standard mechanism of accountability throughout the organization’s workflow.
Creating an internal frame can be done by using flexible and customisable content and quality management software, such as the ECLIPSE Software Suite.
Step 3: Adopting External quality Auditing standards and certifications
The International Standards Organization (ISO) is a respectable entity that offers crucial guidelines and recommendations on the best way to deal with non-conformance. Therefore your organization can adopt recommendations and guidelines in relation to Quality Management Systems to prevent the occurrence of non-conformances from happening.
Sometimes your organisation will be forced to adhere to ISO or other standards such as the ECSS Standards (used in the European space industry). The ECLIPSE Software Suite can enable you to become compliant and increase speed to meet these quality management standards.
Step 4: Using risk analysis tools
Organizations may put resources into better systems that help them to find, analyse, track and manage risks. This will help in identifying potential areas of non-conformity and taking preventive steps to avoid them.
Using a risk management tool such as the eRISK module will help you to identify the key risks that need to be mitigated. For example, it will allow you to record, monitor, assess, and resolve risks quicker.
Step 5: Setting up an accountability framework
An accountability framework will involve setting up a system that will track when things go wrong and identify the players involved in the occurrence of non-conformance.
With this system, you will be able to see which actions have been taken or haven’t been taken. For example, a system that allows for accountability will force parties to mitigate risks before they become non-conformances.
Next to this, when non-conformance reports are created, accountability for actions will allow for faster resolution.
Best practices when implementing both corrective and preventive actions
When executing both there are some important considerations you should put in mind and these include:
- Properly define the non-conformance or risk, understand the details and don’t deviate. Documentation of the issue in a fixed framework can be an essential part to do this.
- Assign the right people to deal with the issue is very important. The people charged with overseeing the organization’s quality management systems should have a broader understanding of the compliance economics of the organization. They should be in a position to communicate easily on actions needed to handle non-conformities.
- Standardise to avoid conflicting procedures in the operational workflows. In other words, the steps taken to deal with non-conformances should be very clear and straightforward without confusing the organisations and teams involved.
- Enable tracking, reviewing and traceability of the entire process. This helps the organization to analyze and understand if the measures implemented in the workflow are correct and whether actions are performed and effectively working. Using a standard monitoring and evaluation mechanism, the organization can achieve its target objectives and mitigate risks that could arise from the occurrence of non-conformances.
Use the ECLIPSE Software Modules to execute corrective and preventive actions effectively
The ECLIPSE Software Modules form an ideal base to implement both corrective and preventive actions within your organisation. The modules will enable you to take into account every important aspect that was mentioned in this article.
The AIM module will help you communicate the actions needed and track progress on actions taken. This will help to improve transparency and collaboration amongst the teams involved in implementing corrective and preventive actions.
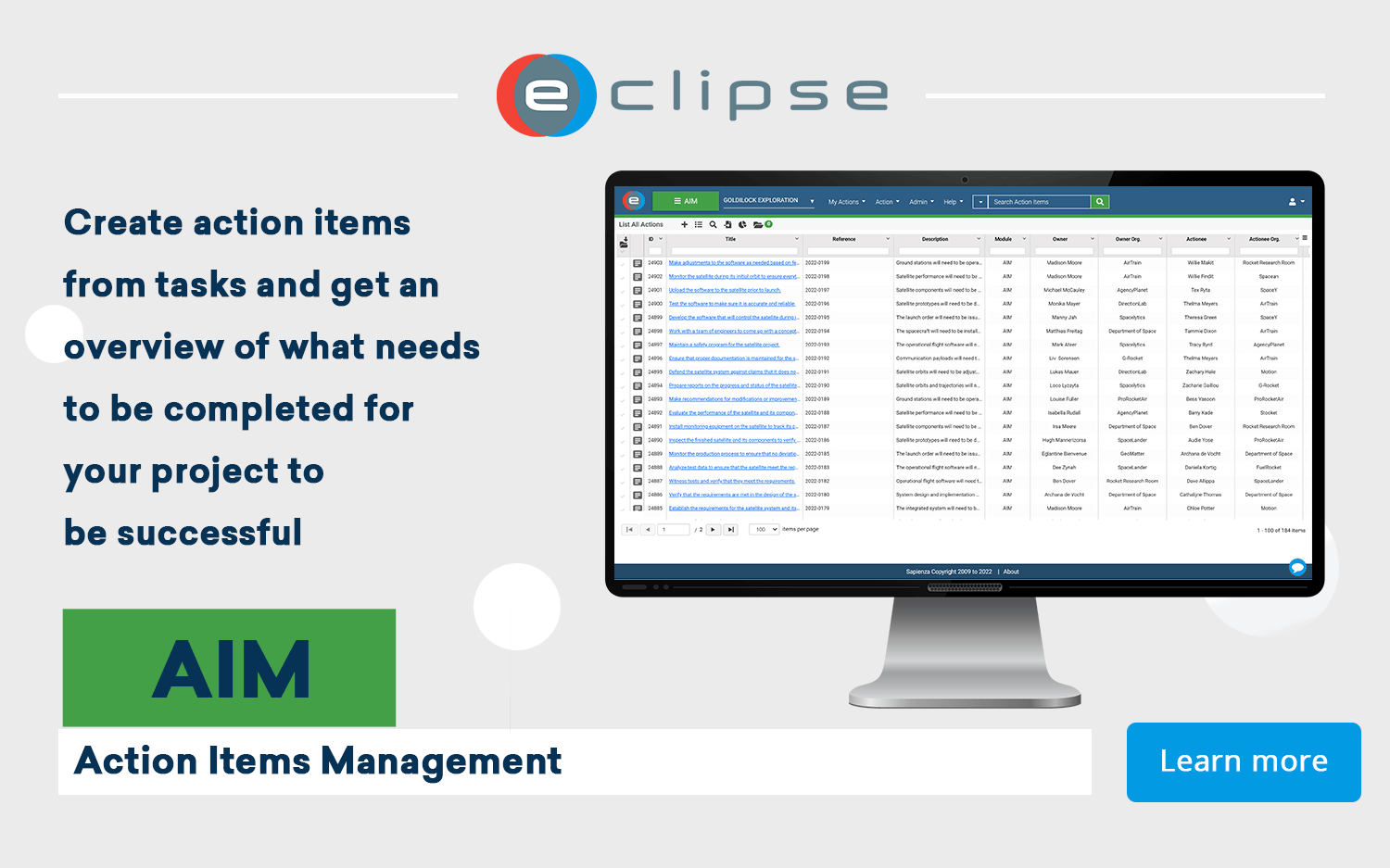
The eRISK module of the ECLIPSE Software Suite will help you to identify risks, find risk trends, assign them to the right people and track their mitigation process. This will help you avoid potential non-conformances and execute preventive actions effectively.
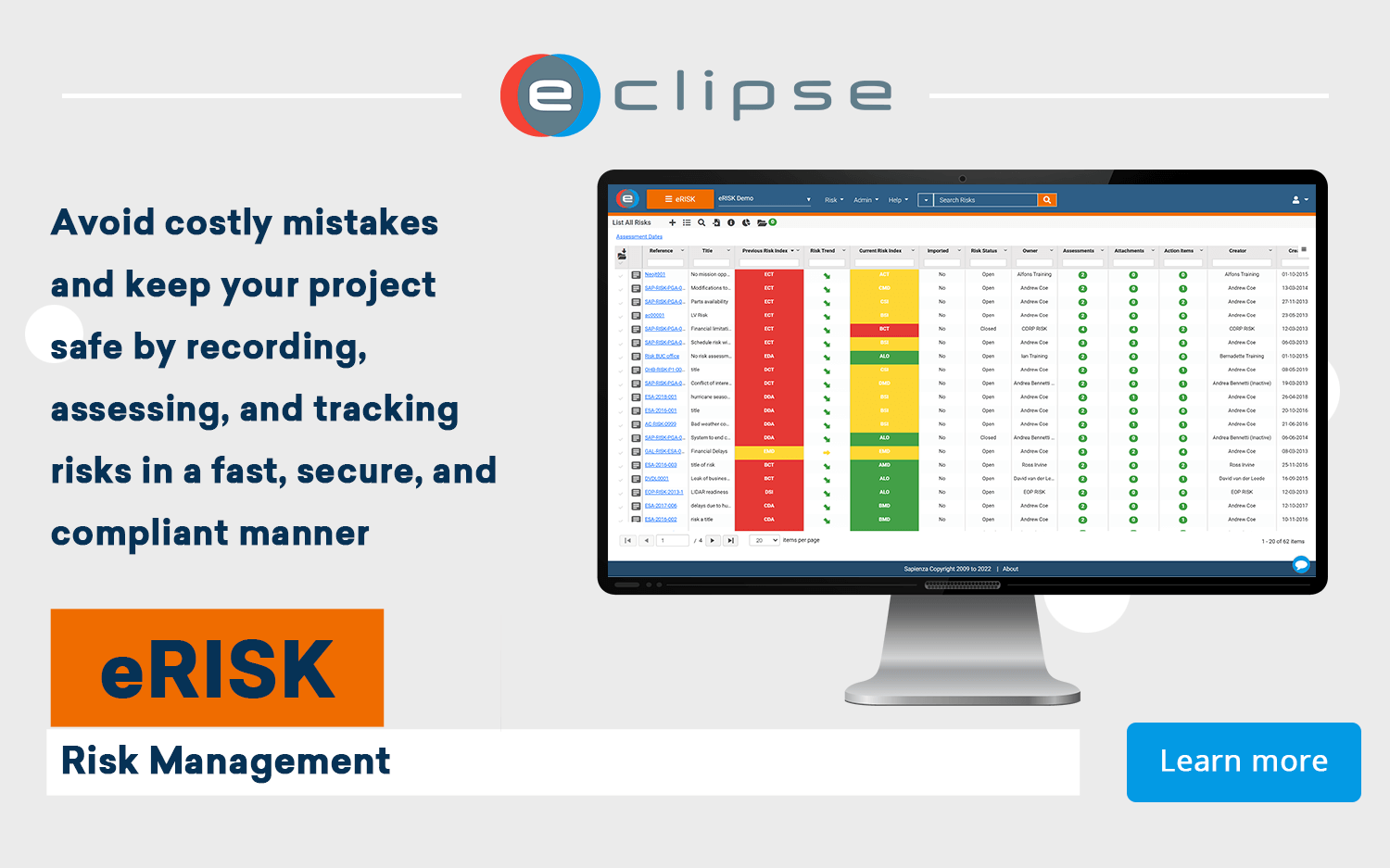
The eNCTS module enables you to create non-conformance reports, and see their status and the actions taken on them. This will help you to manage and resolve non-conformances quickly and efficiently.

The ECLIPSE Software Suite is an excellent foundation to start implementing corrective and preventive actions in your organisation. It will help you to mitigate risks, avoid potential non-conformances and ensure compliance with quality standards.