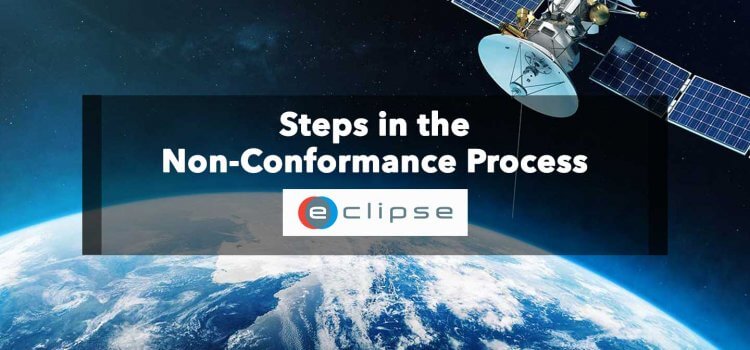
Non-Conformance Process: Steps, Aspects, and More
06 Sep, 2024
A Non-Conformances Process is a set of procedures and processes the team must take to understand the root cause and the best way to deal with a Non-Conformance. Non-Conformance procedures can involve a series of steps that have to be executed. Also, various players within the organization must be involved to facilitate thorough decision-making on the issues that could arise.
How does the Non-Conformances process work?
We have outlined several steps you can take when dealing with a Non-Conformance in your organization.
Step 1: Identification of Non-Conformance
This is the first and foremost step of a Non-Conformances Process. The objective here is to identify Non-Conformances, in other words, any areas within the organization or project that do not meet the standards, specifications, or requirements.
Different factors can cause the identification of a Non-Conformance. For instance, it could result from a customer complaint, rejection, general observation, or an audit. An audit or review can be conducted internally by personnel within the organization, or an external body could do it.
Step 2: Understanding the Non-Conformance
Once you have identified a Non-Conformance, the next step is to investigate and understand what caused the Non-Conformance. The initial analysis will help you properly understand the situation before taking further action.
The investigation aims to register the facts and gather evidence to support the decision-making in the following steps. The research should be able to answer essential questions such as when, where, how, and who.
Step 3: Document the Non-Conformance in a Non-Conformance Report
A Non-Conformance Report is generated, which documents all the relevant information about the issue. The report should contain details that have been or will/can be taken to mitigate the risks associated with the identified Non-Conformance.
Depending on the requirements you have for reporting, the report contains information such as:
- Issue/Non-Conformance title
- Description of the issue
- Details of where and when the problem was identified
- Operational workflows affected
- Associated risks
- Actions taken or recommended
- Additional documents and files
Step 4: Notify the relevant personnel
The next step is to notify the relevant personnel within the organization of the Non-Conformance. This could be the Non-Conformance Review Board (NRB), senior management, or other individuals who must be aware of the issue.
Notifying all relevant parties will help to ensure that everyone is on the same page and are aware of the actions that need to be taken. Not notifying appropriate personnel can lead to a lack of ownership and accountability, further escalating the issue.
Step 5: Perform a thorough analysis
Once the team has been notified about the Non-Conformance, the responsible team should conduct a root cause analysis. The root cause analysis aims to understand why the Non-Conformance occurred and identify any systemic issues that might have led to the problem.
A root cause analysis can be performed using various methods such as the 5 Why’s, Ishikawa diagrams, or cause and effect diagrams.
Communication is critical during this step as it will help ensure everyone is on the same page and understands the problem. The team will typically have meetings, review documents and records, and analyze data.
During interviews with the team, you can ask a series of questions about the Non-Conformance, such as what went wrong, when it happened, and how it happened. By answering these questions, you can start to identify any systemic issues causing the Non-Conformance.
Additionally, it’s essential to review any relevant documentation, such as procedures or process descriptions, to identify the issue. Once you’ve gathered all this information, it will be clear what actions need to be taken to address the root cause of the Non-Conformance.
Step 6: Recommending corrective actions
This step brainstorms a couple of corrective actions to deal with the identified problem. This is where a team of experts offers their insights and advice on stopping the impact of Non-Conformance.
The best-case scenario is that the Non-Conformance that has been identified is minor and could not seriously impact the overall operation of the organization. On the other hand, the worst-case scenario could have a severe impact. For example, the comprehensive operational workflows may have been impacted, leading to severe damages, interventions from relevant authorities, and brand reputation setbacks.
Now, interventional recommendations could be implemented based on the Non-Conformances identified. If it requires a complete overhaul of the entire workflow, then it could mean that the impact caused is likely to be severe.
Step 7: Recommending preventative measures
When you understand what could have caused the Non-Conformance, you can learn from the issue and create preventive measures sure the problem doesn’t happen again in the future. The team could execute a series of measures to futureproof the organization’s workflows and overall operations. This could involve:
- Changing material suppliers
- Updating equipment
- Modifying processes
- Altering packing methods
- Training organization’s teams
- Implementing timely inspection
- Adopting, integrating and standardizing
- Adopting external auditing standards
Step 8: Making final decisions
The management personnel must decide on the final course of action at this step. This will include deciding which corrective and preventative measures will be implemented.
The management team will also need to assign responsibility for ensuring that the corrective and preventative measures are put in place and carried out effectively. In some cases, it may be necessary to bring in external consultants or experts to help with this process.
Once the decisions have been made, actions will be sent down the line to the relevant departments. Everyone must understand what they must do to avoid confusion or misunderstanding.
Step 9: Implementing the corrective and preventative actions
This will usually involve several different departments and team members, so it’s essential to have a clear plan in place.
Each corrective and preventative action must be carried out according to the plan. Once actions are completed, check if they are effective and the problem is resolved.
Step 10: Close out the issue by updating the register accordingly
This is the final stage of the process, where you document everything done to deal with the identified Non-Conformance. This includes updating the Non-Conformance register with new details about the issue, its root cause and how it was handled. The Non-Conformance can now be closed off.
When another Non-Conformance arises, a new cycle of the Non-Conformance Process begins again from the first step.
Want to make Non-Conformance Management easier, faster, and more structured?
Try the ECLIPSE Software Suite
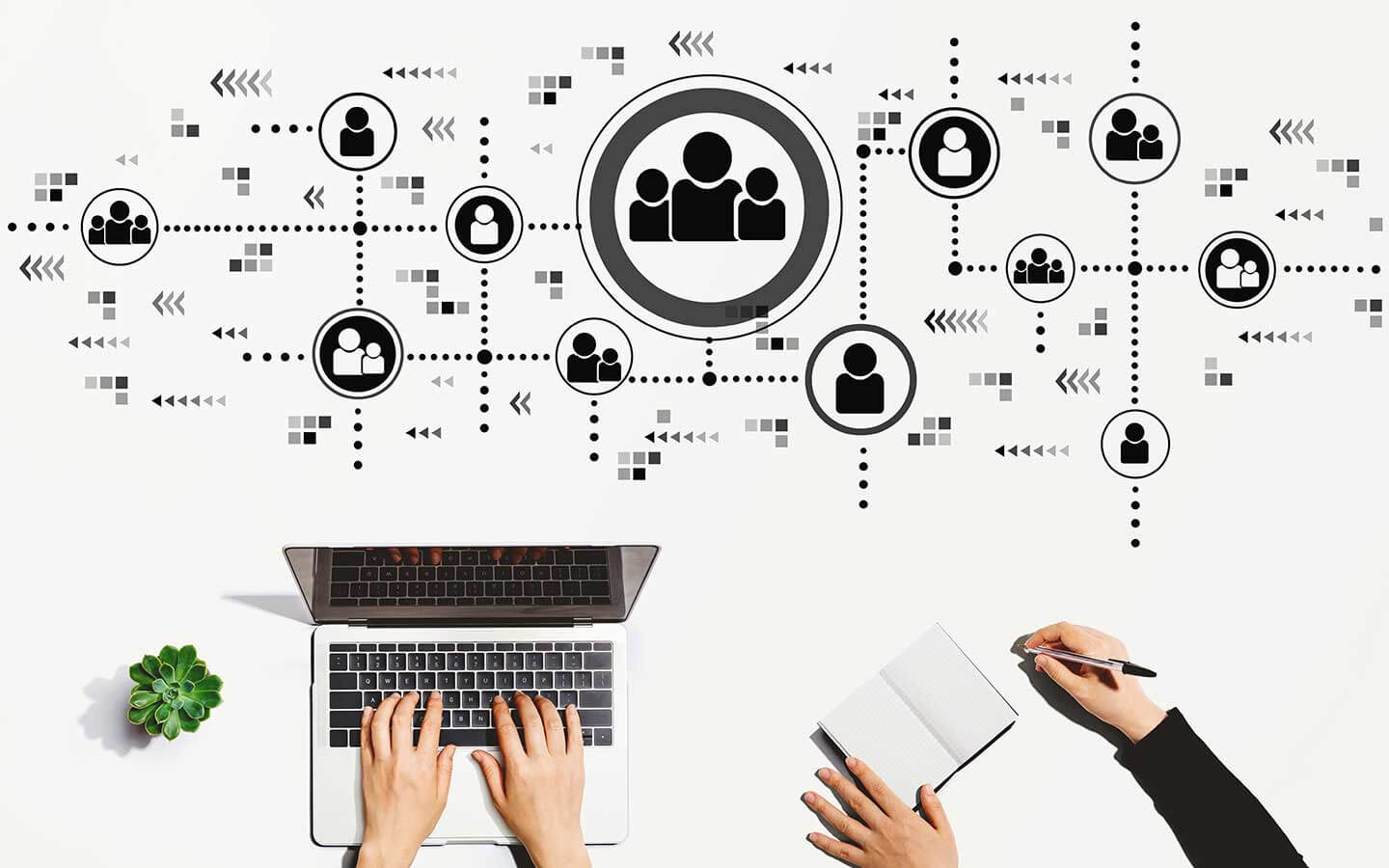
Players in the Non-Conformance Process
The Non-Conformance Process will need to be executed by a series of players. The players required will depend on the size and partners of your organization. Below you find common players in the Non-Conformances Process.
Recorder (identification): A recorder may be any individual within the organization who first identifies the existence of a Non-Conformance. Their work is not necessarily auditing or inspection; they could be employees working with the product or service.
Auditing and Inspection Team (identification): This involves a team of internal inspectors, auditors and department supervisors who oversee the responsibilities assigned to junior employees. At this level, auditors and inspectors or even supervisors are supposed to document the problems related to Non-Conformance and then make a detailed report of their findings.
Non-Conformance Review Board (analyzing and understanding): This is a group of representatives from different departments within the organization. They are responsible for reviewing all cases of Non-Conformance and then making decisions on the best way to solve the problem.
Project Manager or Quality Manager (managing actions): In big organizations, there is always a project manager responsible for ensuring that all Non-Conformance cases are handled as quickly as possible. The project manager also liaises with other stakeholders to ensure that corrective and preventive actions are put in place to avoid a repeat of the problem.
Executive Management (managing actions): Executive management is the overall overseer of the organization’s entire operations. They design new policies aimed at dealing with Non-Conformances. They can also take swift executive measures like punitive actions against responsible supervisors in their respective departments and execute a final decision on what is needed.
At-fault party (action taker): Depending on the severity of the Non-Conformance, there could be an at-fault party who is held responsible for the mistake. Such a party could be a supplier, a contractor or even an organization employee. Typically the at-fault party is expected to support the corrective and preventive measures to ensure that the problem does not reoccur.
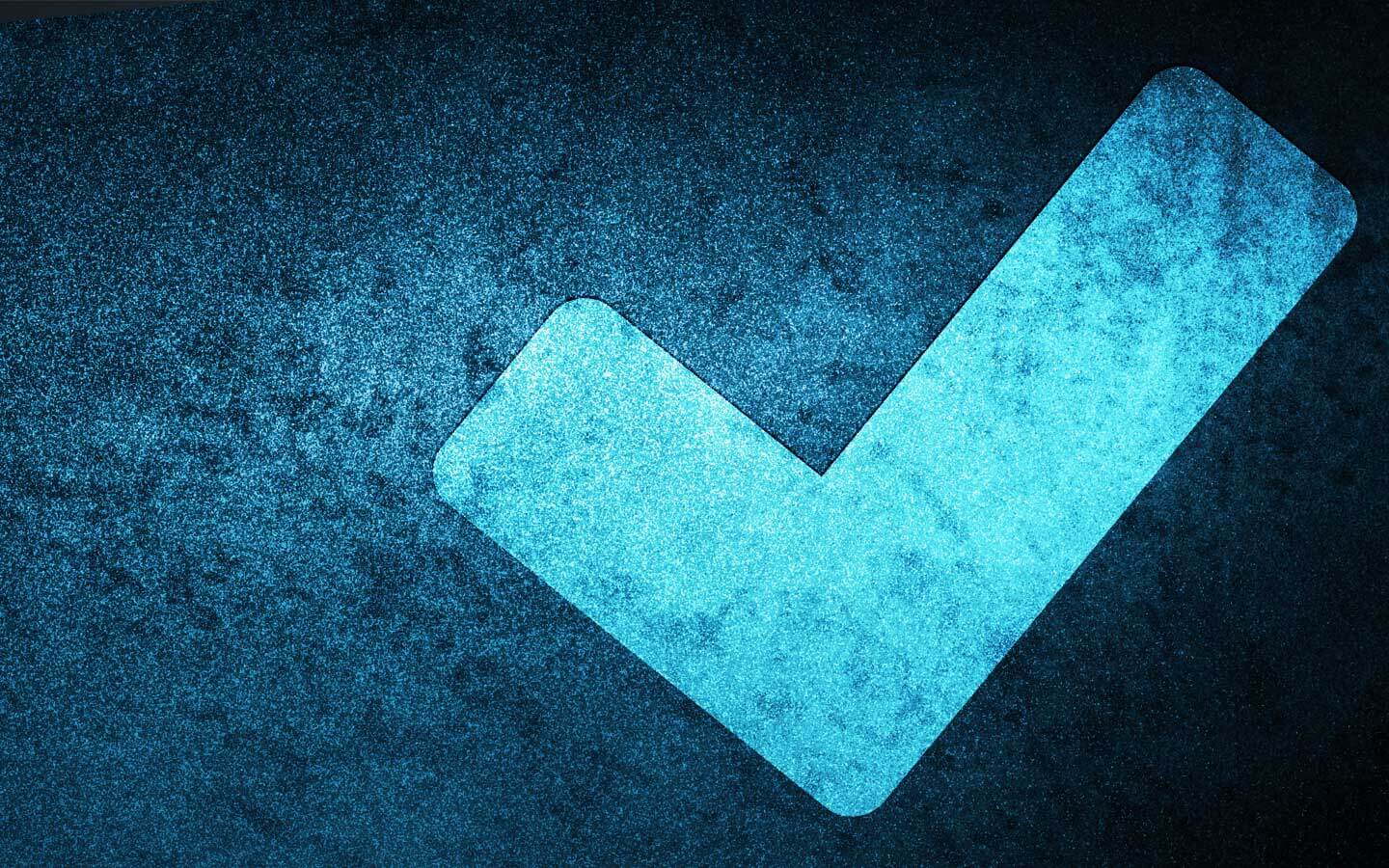
What are aspects you need for a solid Non-Conformances Process?
A couple of distinctive factors can be used to define a good Non-Conformances Process. These include the following:
Customization
Sometimes, you will require customization to ensure that the process fits its purpose. This means that the method above may not fit your company. However, a variation of this process or another similar process may do so. You will have to consider what is required for your specific organization and sector and make slight adjustments where necessary.
Flexibility
Flexibility is another key factor as the process needs to be able to adapt to different types of Non-Conformances. This could include anything from a minor, isolated issue to a much more severe problem that has a major impact on the organization’s operations. The process you use should be able to deal with both types.
Clear responsibilities
Each stage of the process should have clearly defined responsibilities to ensure that everyone knows what they need to do. This will help to avoid any confusion or misunderstanding. Knowing which tasks will be assigned to specific individuals or teams is important.
Timely actions
Once a Non-Conformance has been identified, it’s important to take action to resolve the issue. This may require some team members to drop what they’re doing to deal with the problem, but it’s important to get on top of the issue as soon as possible. Timely actions will help to minimize the impact of the Non-Conformance.
Ability to understand the problem
The team should be able to fully investigate the root cause of the problem, which will help ensure that the issue is properly resolved and doesn’t happen again. Without understanding the necessary details, the problem may not be handled, leading to further challenges within the organization.
Well-documented
Proper documentation of the problem is part of the entire process. Organizations can use a Non-Conformance Report (NCR) which will document every aspect of the anomaly. The right documentation gives a clear and detailed picture of what needs to be done to proceed with the project.
Control over Non-Conformances
There are many different aspects of quality management, one being Non-Conformance Control. Getting control of Non-Conformances can be vital for efficiency and quality within an organization. Not knowing where the issues are or who is dealing with them can be a recipe for disaster.
Precise and accurate procedures
Undoubtedly, a misleading and confusing Non-Conformance procedure could also be catastrophic for the organization. What is needed is the ability to gather accurate information, so crucial decisions are taken and implemented. When the entire procedure fails to live up to its intended objectives, the real issue could fail to resolve.
The Purposes and Benefits of a Non-Conformances Process
As you may know, a Non-Conformances Process is defined as a set of activities carried out when a product, service or system does not meet the requirements. The primary purpose of this type of process is to identify the root cause of the problem, and corrective and preventive actions are put in place to address the issue. But there are other purposes and benefits to be gained from having such a process in place as well.
- Enables the organization to meet regulatory compliance. Many regulatory bodies stipulate specific requirements that organizations must meet. A process for dealing with Non-Conformances helps the organization to stay compliant with these external regulations.
- Aids in the continuous improvement of products and services. The focus on problem-solving helps to improve the quality of products and services.
- Eases working with sophisticated workflows and operational environments. Having a process for dealing with Non-Conformances helps streamline the work process and makes it easier to work with complex operational environments.
- Saves time and money. Tracking issues and addressing them fast can save the organization time and money. Reduces the risk of health and safety issues
- Creates an accountability mechanism. Parties in the organization understand their responsibilities and the consequences of their actions.
- Minimize future operational risks and losses. Such losses could result from a poorly-designed product or misconfiguration of manufacturing processes that would need an entire overhaul.
- Identifies opportunities for the team to learn. They get a chance to improve their skills and knowledge to do their jobs better in the future.
- Increases customer satisfaction. A better non-conformance process will ensure that only conforming products or services are delivered to them.
You can derive many benefits from having a Non-Conformances Process in place. The important thing is to ensure that the process is designed and implemented in such a way that it meets the specific needs of the organization.
Optimise your Non-Conformance Process with Software
ECLIPSE Software Suite’s Non-Conformance Management Software (eNCTS) is designed to streamline the Non-Conformance Process. The software provides a central repository for all Non-Conformance data, making tracking and resolving issues easy.
Want to make Non-Conformance Management easier, faster, and more structured?
Try the ECLIPSE Software Suite

The action/task management tool (AIM) allows users to create and assign tasks, track progress, and view task status at a glance. ECLIPSE Software Suite’s tools are designed to save time and improve efficiency in the manufacturing process. Contact us today to learn more about our products and services.
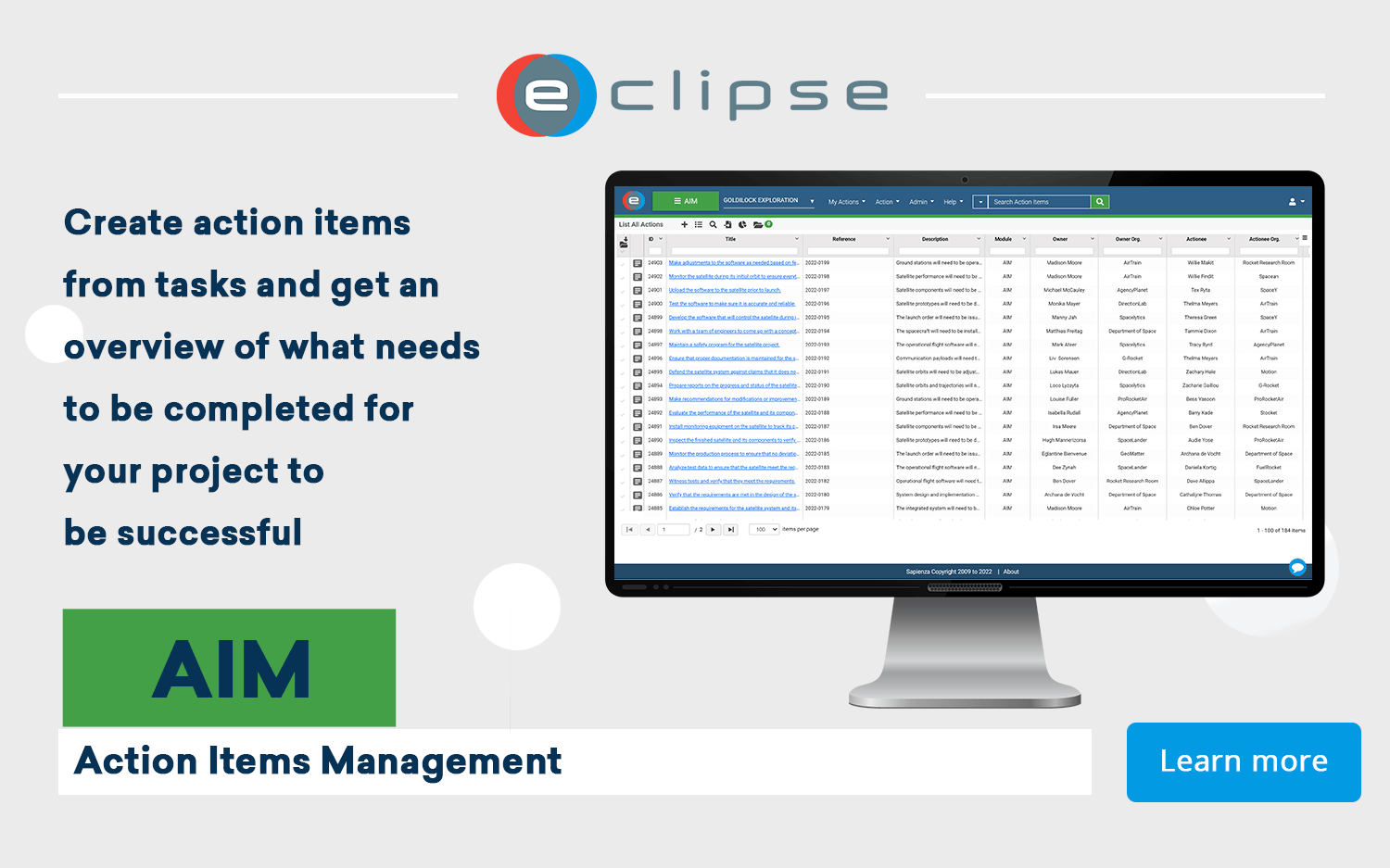